Kanban: A Project Management Approach to Software Development
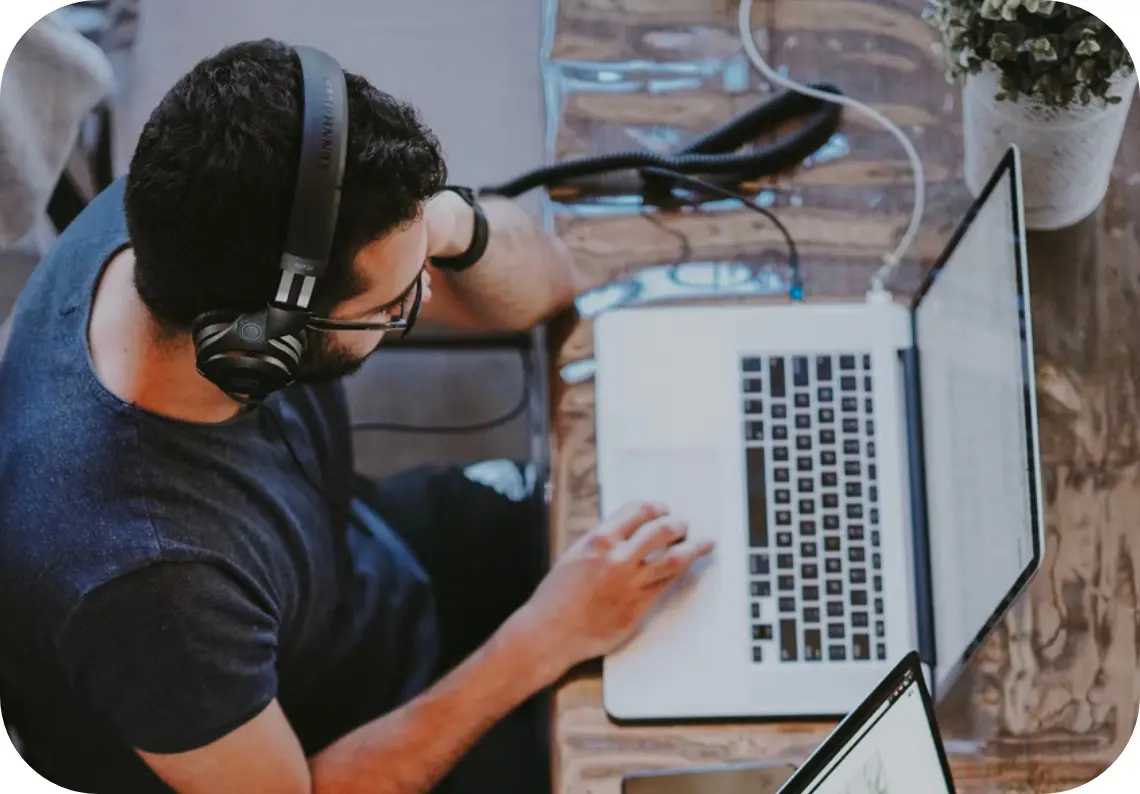
Kanban is a popular agile project management framework. Kanban methodology shares a few similarities with Scrum, primarily in terms of its focus on early release through collaborative and self-management teams.
The origin of the Kanban concept goes back to the production line of Toyota factories during the 1940s.
Kanban methodology is highly visual. This visualization helps develop optimal results by creating a detailed image of the workflow process. Therefore, project teams can identify any bottlenecks during the initial stages of the development process itself.
What is Kanban?
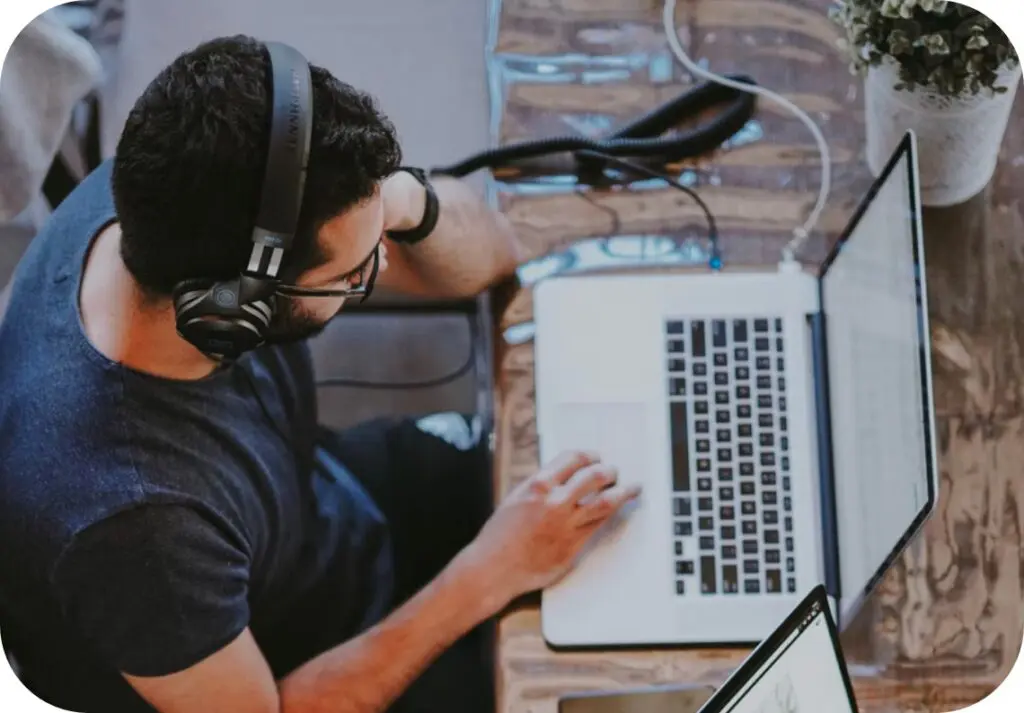
What is Kanban?
Kanban, an innovative project management framework, finds primary use in software development and is equally effective across various industries. It’s a method that revolutionizes how teams and organizations visualize work, optimize the flow of tasks, and strive for continuous improvement.
Originating from the Japanese automotive giant Toyota in the late 1940s, the Kanban approach was initially for managing inventory, emphasizing just-in-time production.
Kanban’s philosophy is deeply rooted in the principles of lean manufacturing. Over time, this approach evolved, transcending its industrial origins to become a versatile tool in project management.
Fundamental Principles of Kanban
At its core, Kanban hinges on a few fundamental principles:
1. Visualizing Work:
Visual management stands at the heart of the Kanban methodology. It serves as a key tool for enhancing transparency, efficiency, and communication within teams.
This principle revolves around the idea that what can be seen can be managed more effectively. In Kanban, visual management is typically embodied using a Kanban board. The Kanban board is a simple yet powerful tool for visualizing work and workflow.
Kanban Board
The cornerstone of visual management in Kanban is the Kanban board. This board is often divided into columns that represent different stages of the work process, such as “To Do,” “In Progress,” and “Done.”
We represent tasks or work items with cards or sticky notes and place them in the appropriate column based on their current status.
This straightforward visualization allows team members to see the flow of work at a glance. This enables quick identification of the bottlenecks and understanding of task progress.
Benefits of Visual Management:
- Enhanced Clarity: By providing a clear visual representation of tasks and their status, the Kanban board helps eliminate confusion and ensures all team members are on the same page.
- Improved Communication: The visual nature of the Kanban board facilitates better communication among team members. It is a focal point for discussions and helps quickly convey information about task progress and priorities.
- Easy Identification of Blockages: Visual management makes it easier to spot bottlenecks and issues in the workflow. This early identification allows teams to address problems before they escalate.
- Fosters Team Collaboration: The visual representation of work encourages collective ownership and accountability. Team members can see how their work fits the larger picture and collaborate more effectively.
- Facilitates Continuous Improvement: The ongoing visibility of work processes enables teams to identify improvement areas and make real-time adjustments. This continuous feedback loop is essential for iterative and incremental improvements.
Adaptability of the Kanban Board: One of the strengths of the Kanban Board is its adaptability. We can customize it to fit any team’s specific workflow and needs, regardless of the industry or type of work. Whether a physical board with cards or a digital tool, you can tailor the Kanban board to enhance visibility and control over work processes.
In conclusion, visual management is a fundamental aspect of the Kanban methodology, providing a clear, visual way to track work progress, facilitate team communication, and drive process improvements. Its simplicity and effectiveness make it an indispensable tool in the arsenal of agile project management
2. Limiting Work in Progress:
By restricting the number of tasks in progress simultaneously, Kanban ensures that project teams maintain the focus to maximize efficiency. This approach reduces the overburdening of team members and fosters a more manageable workflow.
3. Enhancing Flow:
Kanban emphasizes smooth workflow management. It encourages teams to monitor the pace of work and make adjustments to improve overall efficiency. This might involve redistributing tasks, reallocating resources, or modifying processes.
4. Explicit Process Policies:
Clear guidelines and rules govern the Kanban process. This clarity ensures that everyone on the team understands their responsibilities and how to handle various tasks.
5. Feedback Loops:
Regular meetings and feedback sessions are integral to the Kanban process. These gatherings allow the team to reflect on their progress, discuss challenges, and plan for future improvements.
6. Collaborative Improvement:
Kanban is not just a methodology but a mindset of continuous improvement. It encourages teams to constantly seek ways to enhance their workflows, processes, and outcomes, fostering a culture of perpetual evolution and adaptation.
Enhancing Collaborative Development with Continuous Improvement in Kanban
While discussing the fundamental principles of Kanban, it’s pivotal to intertwine the concept of continuous improvement with collaborative development. These two aspects, though distinct, are deeply interconnected in the Kanban methodology.
- Synergy of Collaboration and Improvement: In Kanban, collaborative development is not just about working together but also about evolving together. Teams are encouraged to regularly reflect on their processes, discuss challenges, and seek solutions collaboratively. This approach naturally fosters an environment of continuous improvement, where the focus is not only on completing tasks but also on enhancing how we carry out the tasks.
- Feedback Loops as Catalysts: Regular meetings and retrospectives are crucial in this process. These are not just status updates but opportunities for the team to engage in open dialogue about their workflow, identify inefficiencies, and brainstorm potential improvements. By leveraging these feedback loops, teams can continuously refine their processes, enhancing both productivity and output quality.
- Empowering Team Members: Continuous improvement in Kanban also emphasizes empowering every team member to contribute to process improvements. This democratic approach ensures that insights and suggestions come from diverse perspectives, leading to more effective and comprehensive enhancements.
- Integrating Continuous Improvement into Daily Work: Rather than viewing improvement as a separate activity, Kanban embeds it into the daily workflow. The focus is on encouraging the teams to implement small, incremental changes regularly rather than waiting for a major overhaul. This approach makes improvements more manageable and less disruptive, leading to a more agile and responsive workflow.
- Visual Tools as Improvement Aids: Using visual management tools in Kanban – like the Kanban board – further supports continuous improvement. These tools not only help in tracking the progress of work but also in visualizing the workflow and identifying areas for improvement.
In summary, integrating the concept of continuous improvement with collaborative development enhances the overall effectiveness of the Kanban methodology. It shifts the focus from merely completing tasks to constantly improving how we approach these tasks and execute them, fostering a culture of perpetual growth and adaptability.
Historical Background of Kanban
Before we go deeper into Kanban project management and its benefits, let’s dig deeper into the historical background of Kanban:
The Birth of Kanban in Post-War Japan
In the aftermath of World War II, Toyota, a burgeoning Japanese automotive manufacturer, embarked on a mission to revolutionize its production processes.
This era marked the genesis of the Kanban system, a concept that would eventually transform global manufacturing and project management methodologies. Toyota’s objective was to optimize efficiency and minimize waste, a challenge that led to conceptualizing a new, agile approach to production.
The inspiration for Kanban originated from an unexpected source – the supermarket retail system.
Inspired by how supermarkets restocked items based on consumer demand rather than supplier availability, Toyota engineers saw potential in applying a similar approach to managing factory inventory. This observation laid the foundation for a demand-driven production strategy, contrasting the prevalent mass production models of the time.
Kanban’s Implementation at Toyota
At its core, the Kanban system implemented at Toyota was a visual management tool revolving around using physical cards – Kanban cards.
These cards traveled with parts and components throughout the factory, signaling the need for replenishment or indicating the completion of certain production stages. This visual cue system enabled workers to easily understand production needs, aligning the manufacturing process closely with actual demand.
This new method was a significant departure from traditional manufacturing philosophies. It introduced the principles of the “just-in-time” manufacturing process.
The “just-in-time” process focuses on procuring and producing exactly what we need at a particular time.
By implementing Kanban, Toyota could significantly reduce waste and inefficiency, enhance productivity, and reduce costs, setting a new standard for lean manufacturing.
Evolution and Global Adoption of Kanban
From its roots in Toyota’s factories, Kanban underwent a remarkable evolution. By the early 2000s, it started to gain popularity in the software development sector, appreciated for its flexibility and efficiency in managing complex projects.
The core principles of visualizing work, limiting work in progress, and ensuring continuous flow found a new application in this field, far removed from automotive manufacturing.
Today, Kanban has become a versatile and effective project management tool for various industries beyond automotive and software. Its visual management principles, demand-driven workflow, and continuous improvement have proven universally applicable and effective.
Kanban’s journey from a simple inventory management tool to a comprehensive project management methodology demonstrates the enduring value of innovation and adaptability in business processes.
“When” and “Why” Kanban”?
Kanban’s beauty lies in its simplicity and flexibility.
Unlike some project management methodologies that are rigid and prescriptive, Kanban allows teams to customize its principles to best fit their unique contexts and challenges. This adaptability makes it an invaluable tool for teams striving to improve their productivity and efficiency in a rapidly evolving work environment.
Kanban is highly adaptable and ideal for projects of varying sizes, from small teams needing a flexible approach to larger, more complex endeavors. Its visual management principles and continuous flow make it effective in diverse contexts, including enhancing personal productivity.
Why Is Kanban Helpful?
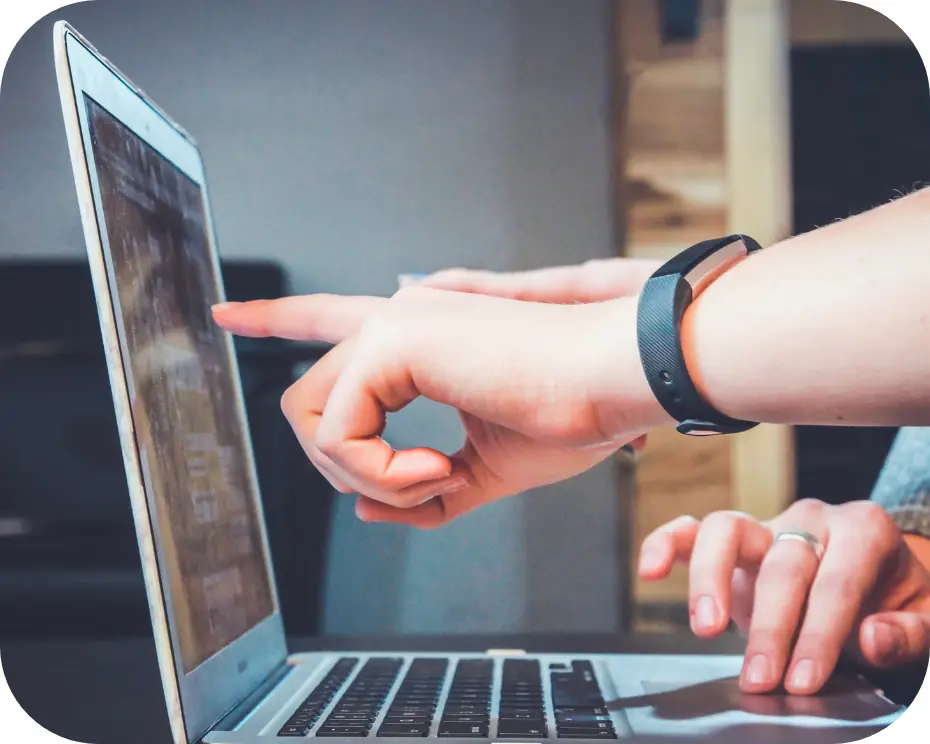
- This IT project methodology is incredibly simple to use and understand, making it practical for any organization.
- It enables continuous and sustainable improvement in different functions of the company, making the analysis of work easier than before.
- Any extensive venture requiring continuous and ongoing changes benefits from the Kanban approach because it promotes maximal adaptability.
- Improves collaboration and ensures the entire team works together to obtain the ideal outcomes while reducing the overheads.
- It also reduces costs and wastage by highlighting issues within processes and eliminating them.
Limitations
- On the downside, Kanban cannot connect autonomously, and usually, we need to combine it with other forms of workflow frameworks.
- Kanban’s basic assumption is that the plans are consistent and stable to a certain extent. Therefore, it is not ideal for industries and organizations of businesses with a dynamic environment.
- There is neither room for iteration in Kanban nor specific timeframes for every phase of product development management.
Steps To Follow
Kanban’s popularity has increased with the ever-increasing popularity of remote working culture and implementation of the agile and lean framework across different sectors. Here are the different steps for its successful implementation.
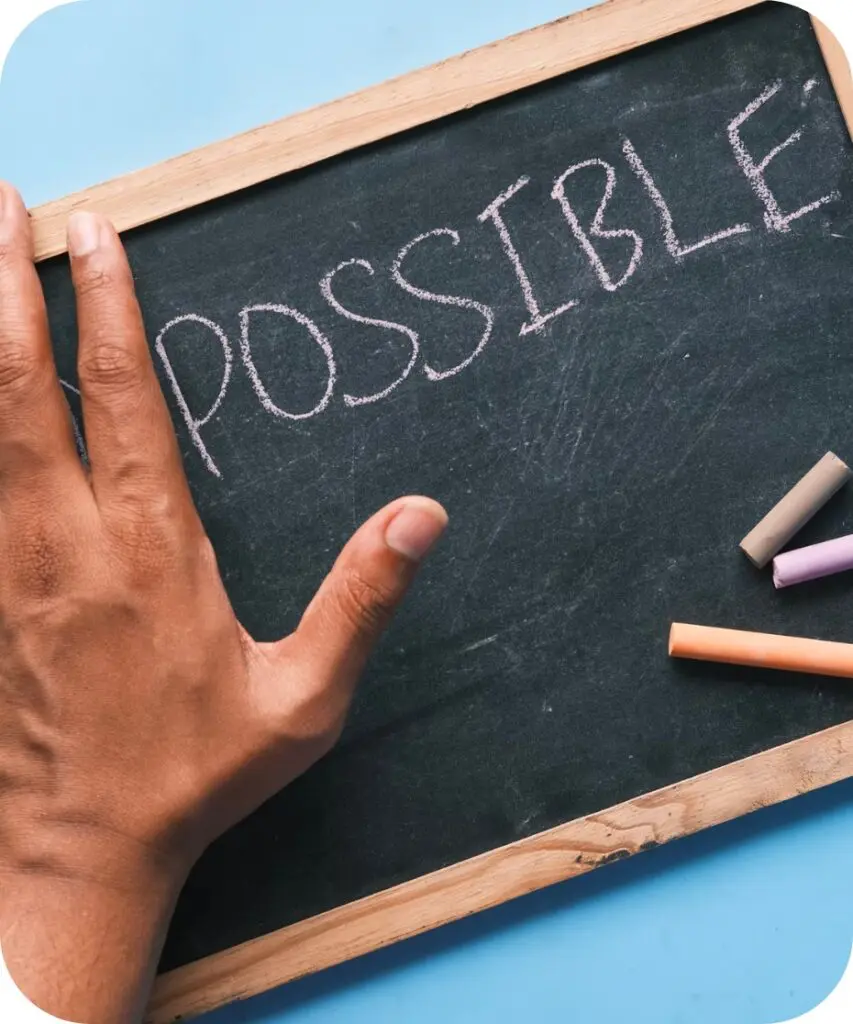
Step 1: Map The Existing Workflow
Identifying the different processes in your existing workflow is the first step to implementing the Kanban system. It needs the participation of every member of the team. The primary point of discussion is to understand how any work, task, or process can move from “to do” to “done” stages. The three things to consider are as follows:
- Are there any specific steps or processes a task must go through before completion?
- What are the handoffs, and where do they occur?
- Is there any scope for a review cycle built into the process?
The three states to categorize all tasks can be: “to do,” “doing,” and “done.” However, we can customize this as per the needs and requirements of the team or the goals.
Step 2: Visualize The Work
Once the mapping of the entire process is over, visualize the workflow. Consider all the existing and active work items and any upcoming ones. After this, visualize each item on the Kanban board by creating a specific card for them.
The cards’ details don’t have to be filled in and can be done later. As of now, the goal is an exercise in visualization for the entire team to understand how the work must flow.
Even a seemingly simple task takes time and mental capacity and keeps the team from doing other tasks. The Kanban system will not be helpful unless it truly reflects your team’s capacity and processes. So, we must include all tasks, even the seemingly small ones.
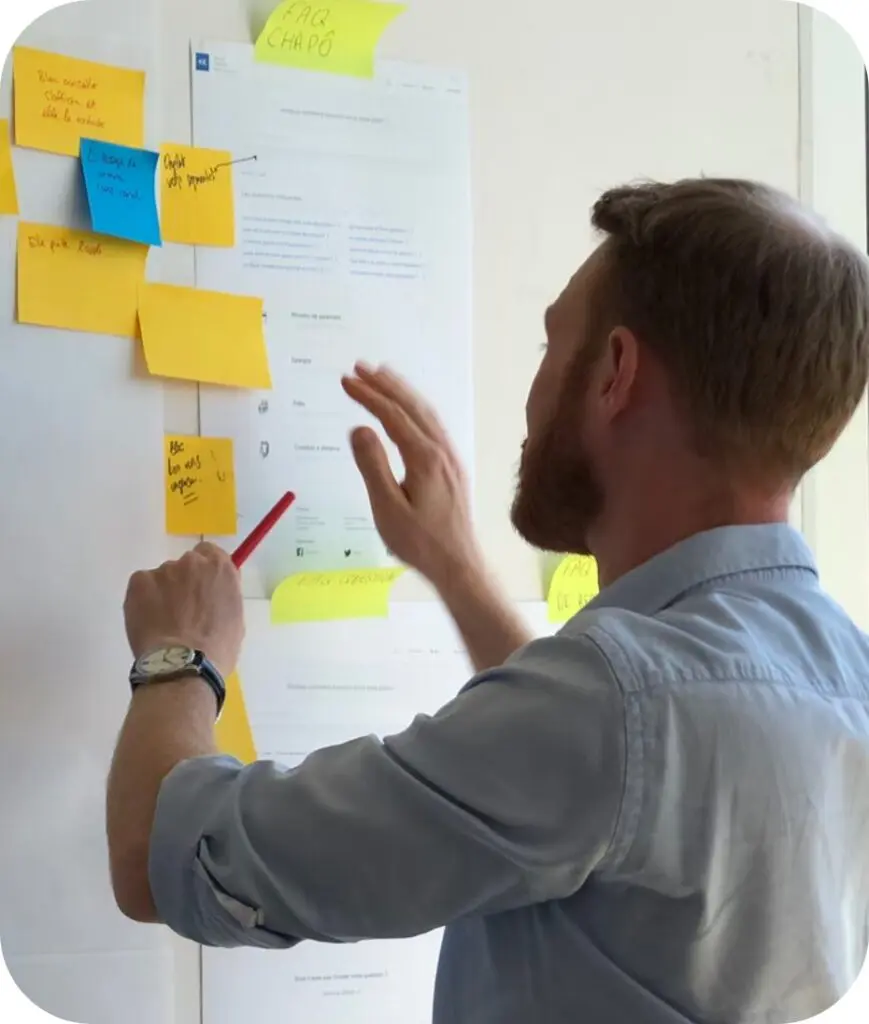
Step 3: Concentrate On the Flow
How smoothly work progresses through a system is known as flow. Good flow ensures the work moves from one step to another without delays or disruptions.
Kanban offers a visual representation of the workflow, making it easier to notice any opportunities for development and improvement. It helps identify any possible bottlenecks, challenges, or obstacles, enabling better and quicker problem-solving.
This is the stage for prioritizing processes’ optimization by utilizing the available information. Any changes that must be made with any of the processes to be followed or completed must be done here.
Step 4: Limit WIP
The next step is to adopt a crucial concept of the Kanban framework — limiting work-in-progress (WIP). This results in improved quality of work, smoother handoffs, reduction in context switching, and quicker results.
The number of cards that belong to the Kanban board’s active or “doing” column is the WIP. These limits must be set at team and individual levels. Doing this improves the productivity and efficiency of your team and ensures each individual is focused on delivering work of optimal quality while eliminating unnecessary distractions.
Step 5: Manage And Measure
Do not forget the need for constant change, improvement, and evolution to make the most of Kanban’s principles. It is not a one-time process, and we must follow and optimize it regularly to maximize value and productivity from the Kanban system. To do this, flexibility and an open mindset for improvement are needed.
Measuring and analyzing different teams’ performance is an excellent means to ensure continuous growth. Lead time and cycle time are two basic metrics that can be used to obtain actionable insights into improving a team’s performance.
Conclusion
The processed-based management system of Kanban enables teams to visualize the entire workflow thoroughly. It also helps improve communication and enhance overall productivity and efficiency.
Organizations can use Kanban to improve their teams’ efficiency, whether a global giant or a small start-up. Whether manufacturing, fashion, technology or even finance, Kanban is house full. Some of the world’s most renowned names, such as Toyota, Pixar, Spotify, Zara, and Apple, have revolutionized their workflow processes using Kanban.
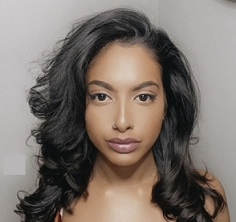
Nisha Arya is a Data Scientist and Technical writer from London.
Having worked in the world of Data Science, she is particularly interested in providing Data Science career advice or tutorials and theory-based knowledge around Data Science. She is a keen learner seeking to broaden her tech knowledge and writing skills while helping guide others.